In the production process of lithium batteries, plane burrs and end face burrs are common quality problems, which not only affect the appearance quality of the battery, but also may have a serious impact on the performance and safety of the battery. We analyze the difference between flat burrs and endface burrs of lithium batteries and their causes, discuss the impact of these two types of burrs on the performance and safety of lithium batteries, and propose a series of effective solutions, aiming to provide a reference for the quality control of lithium batteries in the production process.
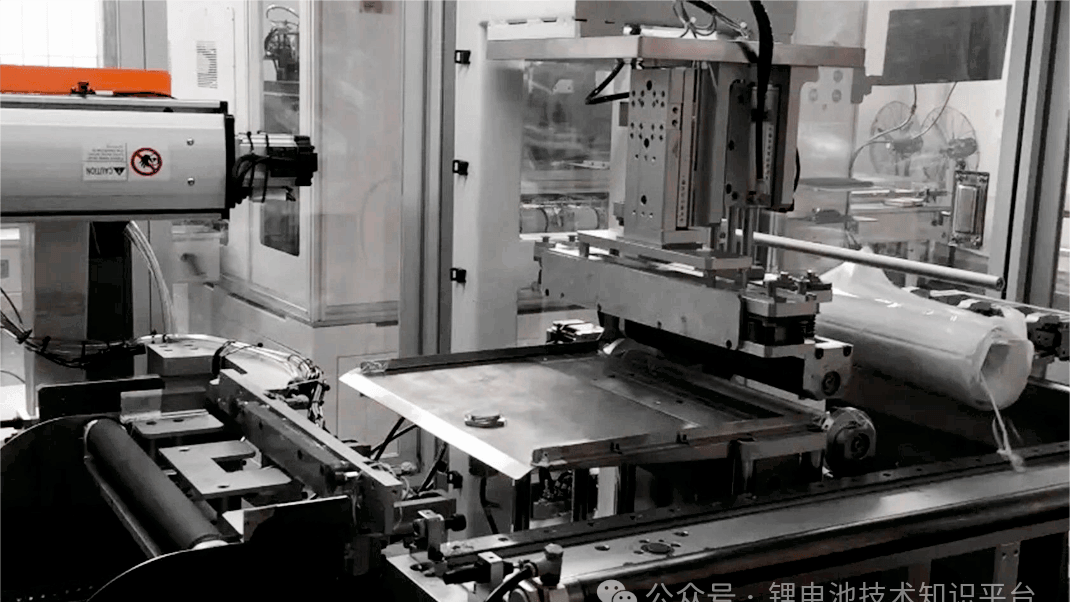
2.Second, lithium battery plane burr and end face burr difference
Plane burr
The plane burden refers to the burrs formed by the plane part of the lithium battery. In the production process of lithium batteries, the polar sheets need to undergo multiple segments and tailors. The unreasonable parameter settings, tool wear, and material problems in these processes may cause the plane burden. The generality of the plane burrs is high, and there will be different degrees of plane burden problems in each production batch.
End surfacebridge
The end surface burr refers to the burrs formed by the end surface of the lithium battery pole. Similar to the plane burr, the production of the end surface burrs is also related to factors such as production technology, tool wear, and material properties. Due to the special position of the end surfacebrid, once it is formed, it is difficult to eliminate it through simple follow -up processing, so its universality is relatively high.
3.The effect of lithium battery plane and end surface burrs on performance and safety
Effect on performance
The existence of the plane burr and the end surfacebrid will cause the internal resistance of the lithium battery to increase, thereby reducing the battery’s charging and discharge efficiency. At the same time, the burrs may also pierce the internal diaphragm of the battery, causing the battery to be short -circuited, which further affects the performance of the battery.
Effect on security
The existence of the burrs may pierce the diaphragm inside the battery, causing a short circuit inside the battery, which causes safety accidents such as thermal loss of battery, combustion, and even explosion. In addition, the burr may also cause problems such as leakage and flatulence during the charging and discharge of the battery, which further threatens the safety of the battery.
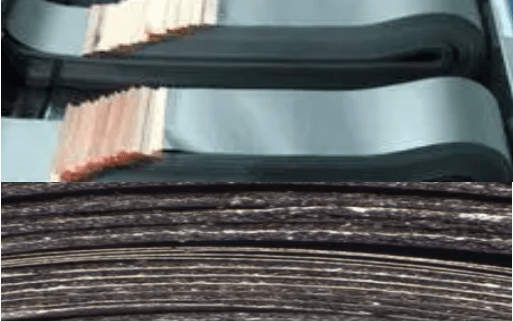
4.solution
Aiming at the problem of lithium battery plane burden and end -facial burrs, solutions can be proposed from the following aspects:
Optimize production process parameters
By adjusting process parameters such as cutting and breeding, such as cutting speed, cutting depth, and blade gaps, it can effectively reduce the generation of the burrs. At the same time, check and replace the tool regularly to ensure the sharpness and accuracy of the tool, and it is also an important measure to reduce the burrs.
Improvement of material performance
Materials with high shear strength and easy processing can effectively reduce the generation of burrs. In addition, surface treatment of materials, such as coating lubricants, can also reduce the chance of the formation of the burrs.
Strengthen quality testing and control
Strengthen quality testing and control during the production process, and timely discover and deal with the problem of burrs, can effectively avoid the effects of burrs on battery performance and safety. At the same time, the establishment of a comprehensive quality management system and traceability mechanism is of great significance for improving product quality and market competitiveness.
R & D new processing technology
With the advancement of technology and the continuous emergence of new processing technologies, research and development of new technologies suitable for lithium battery pole processing, such as laser cutting, water knife cutting, etc., can fundamentally solve the problem of the burrs. These new processing technologies have the advantages of high precision, high efficiency, low damage, etc., and can significantly improve the production quality and efficiency of lithium batteries.
5.in conclusion
Lithium battery plane burdens and end surface burrs are common quality problems in the production process, which can also have an important impact on the performance and safety of batteries. By optimizing production process parameters, improvement of material performance, strengthening quality testing and control, and research and development of new processing technology, it can effectively solve these problems and improve the production quality of lithium batteries.